What are industrial shredders and what they are made for
What are industrial shredders?
Industrial shredders are useful machines for reducing the volume of bulky solid urban and industrial waste. Shredders play an important role within the recycling companies as they are able to treat a wide variety of waste materials such as, for example, scrap metal, aluminium, copper, brass but also materials such as plastic, paper, wood, tires and food waste.
Thanks to their usage versatility, industrial shredders are machines that are essential for recycling centres, landfills, car demolitions and all entities that work in the field of waste management and recycling.
The categories of industrial shredders
The great versatility of these equipment depends on the different components that make up them and which, based on the structure, are bound to the processing of certain materials.
There are four main drivers that must be taken into consideration in choosing the shredder according to its final usage:
- Nature of the processed material;
- The quantity of material that has to be treated;
- Size of the material required after the shredding;
- Presence or not of foreign material (that has not to be shredded);
- Structure of the shredder.

The nature of the material that will be shredded permits to divide the shredders according to their usage. A machine that will have to shred plastic will have a structure linked, for example, to the size, number of shafts and blades necessary for shredding, different from that of a shredder dedicated to crush wood. The features of each machine are based on the characteristics of the material that will have to be shredded.
Types of industrial shredders dedicated to the disposal of all types of urban and industrial waste produced by human activity can be identified.
Thanks to the possibility of customizing the different components, it is possible to create an industrial shredder for almost all the materials created artificially. There are shredders dedicated to the crushing of plastic and rubber, tires, all household and industrial electronic waste, paper, cardboard, wood and bulky waste, food waste and all special industrial substances, such as filters for oil, hospital waste, metal and textile waste.
The quantity of material to be treated can influence the choice of the type of the industrial shredder to be adopted. For small volumes it is possible to think about a manual loading of the shredder when the hopper allows it. If necessary, platforms can be used to allow the operator to safely load the machine, but from a more suitable position. For larger volumes, automatic loading systems can be used such as conveyor belts, tippers or, if necessary, polyp loaders or mechanical shovels.
Another important driver for the choice of the machine is the size of the material required after the treatment. If the only necessity and the volumetric reduction of the material, the best choice is a double shaft shredder (also called bi-rotors) that can treat even very tough materials with high production.
If, on the other hand, a defined size is needed, single shaft shredders are the right shredders (also called single-rotor or grinders) that allow to obtain a calibrated size thanks to the installed grid that acts as a sieve. Only the material in size suitable for the passage of the material in the grid can come out of the machine. An alternative to single-shaft shredders are the four-shaft shredders that have the option of mounting a grid as well. The latter solution is more suited to tough materials that require treatment with controlled output sizes such as WEEE, tires and special materials.
The other factor that can determine the choice of the type of shredder is the presence or absence of foreign material which has different effects depending on the type of shredder used. In the double-shaft and four-shaft shredders the presence of not crushable bodies can cause the blades to break with consequent downtime which can be long and costly to solve. On the other hand, in single-shaft shredders the damage can be limited to a few tools to be replaced in a short time and at low costs.
The structure of the industrial shredder, and in particular the number of trees that compose it, can perform the function of a further categorization element of the shredders. On the basis of the number of blade holder shafts it is possible to identify single-shaft, double-shaft and four-shaft shredders.
The industrial single-shaft shredders are machines with a solid and customizable structure according to the needs of use. The customization of the machine usually involves the dimensions of the blades that are mounted on the shredder shaft, the dimensions of the installed grid as well as the rotation speed of the rotors. The size of the blades is determined by the type of the material to be treated by the shredder. The possibility of customization and the sturdiness of the structure guarantee the maximum production capacity of the machine and its durability over the time.
The shredders that have a double shaft structure are designed to intervene on large waste, with the final aim of drastically reducing the initial volume. Compared to the above mentioned model, the double shaft shredder has a double blade system capable of turning in the opposite direction, thus favoring the destruction of the material itself. Finally, the four-shaft shredders are the latest generation shredders category. This last type of industrial shredders consists of four shafts equipped with steel blades for crushing the material, which takes place in the most effective way possible as for double shafts but ensuring a selection of the size of the output material as in single shafts.
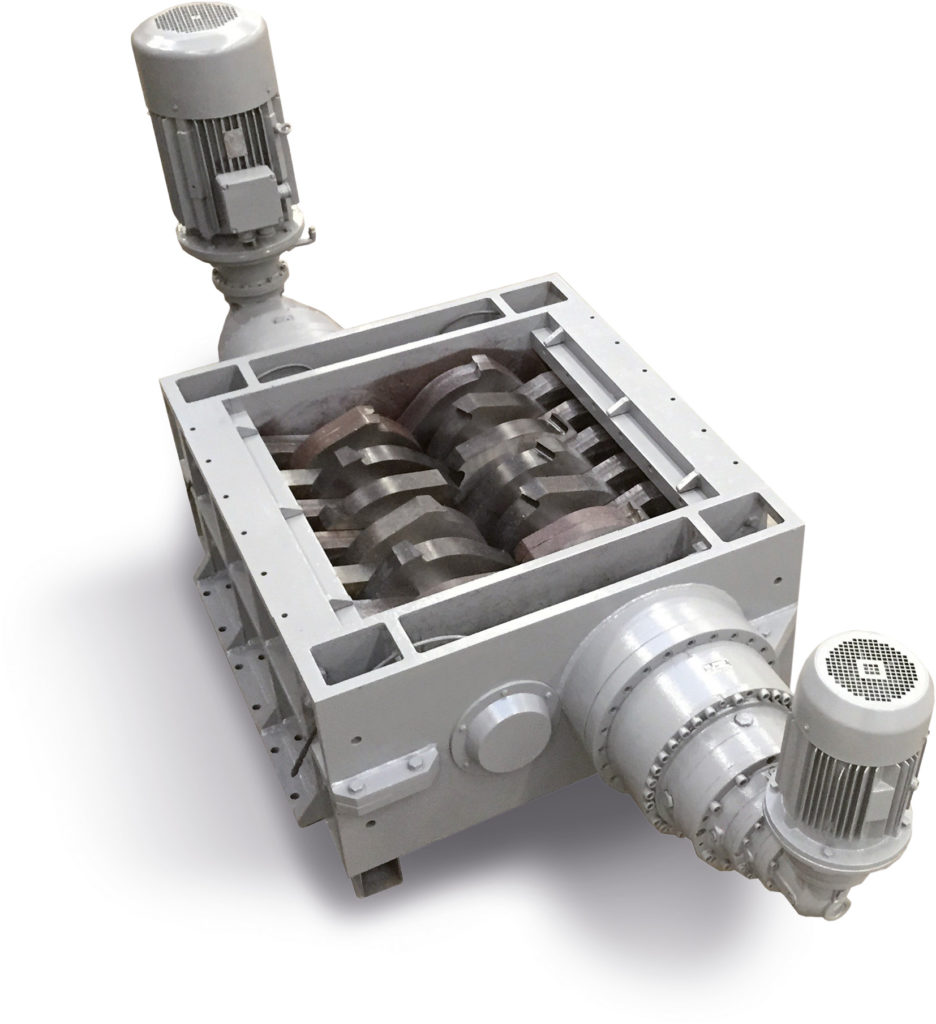
Two-shaft shredder
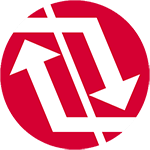
Discover the machines and turnkey plants for recycling different materials.
The shredding process
Components
The industrial shredders, used in recycling systems and plants, have mechanical systems through which the supply of materials and the processing of waste is ensured.
The wastes that arrive at the various shredding plants are sorted before being shredded. The aim is to obtain homogeneous and compatible batches between them, to avoid putting into the recycling plant containers with liquid residues, canisters containing gas and substances that by their nature could encourage the formation of fires that would damage the plant and cause damage to the surrounding area.
Moreover, shredding operations are carried out in a dedicated environment, equipped with appropriate safety, fire prevention, air extraction and purification systems.
Once shredded, the different wastes become part of specific mixtures made for waste recycling plants according to the needs of the plants themselves.
The shafts containing the blades are the basic elements of the structure of industrial shredders for shredding different materials. However, irrespective of the number of shafts, each shredder consists of fundamental parts that accompany the waste from the first stage of the shredding process to its conclusion.
The material to be shredded is sent by gravity or by means of a conveyor belt. In general, the mass of waste to be shredded is loaded by means of a crane with a hydraulic arm. The shredded product is ejected by gravity, under which there is a conveyor belt that advances the product to the depot or to the means of transport, such as lorries.
The central part of the shredder is usually made up of shafts with attached blades; in particular, as mentioned above, there can be one, two, three or even four shafts. Single-shaft shredders are usually composed of: a hydraulically operated ram box that pushes the material towards a tool-holder roller which, thanks to its rotation and the action of a counter-blade, pre-breaks and grinds the material. The product is screened by a perforated grid which determines the final size of the ground material.
Two-shaft shredders, on the other hand, consist of two shafts with rotating blades and spacers. Once the material has been introduced into the hopper and the system has been started up, the shredder picks up and coarsely cuts the waste. The operating system of the two-shaft shredder consists of: a loading hopper and two shafts with cutting elements consisting of disk cutters fitted with hooks. Each hook has the function of hooking the product and dragging it to the cutting stage, made possible by the action of the two counter-rotating shafts. The spacing combs keep the tools clean and facilitate the unloading of the material.
Four-shaft shredders, on the other hand, consist of an input hopper, a four-shaft shredding unit with cutting elements consisting of sharp-edged discs fitted with hooks, and a screen to control the particle size. The largest pieces of waste are returned for further shredding. There is usually a safety device that temporarily reverses the movement of the blades, preventing any structural overloading or breakage of the machine in the presence of an excessive amount of material being taken up.
Depending on the way in which the material is shredded it is also possible to identify different types of shredders such as granulators and grinders. We have a different output dimension, even if both of them are shredders with rotating blades, designed to carry out the grinding and reduction of heterogeneous plastic waste. The use of special steels for the construction of the components makes them ideal for processing even the most difficult materials. The cutting system guarantees energy savings and a significant reduction in dust formation during the waste treatment process. Maximum performance, energy savings and ease of handling.
Pre-shredding
It consists of primary shredding operations, to break up the bags and homogenise the waste, and primary deferrization on the shredded material. The treated waste is dumped on the ground in a collection box from where it is then sent for biostabilisation in a biotunnel.
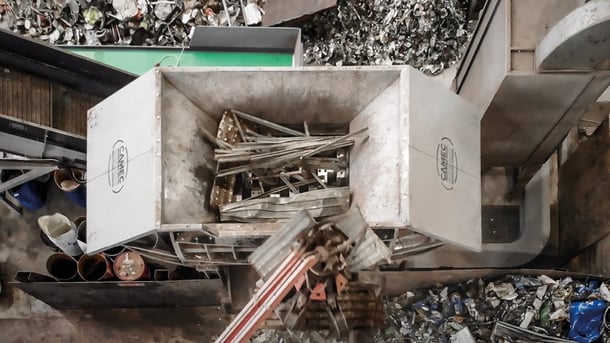
Screening
It is performed by means of an octagonal rotary screen or a disk screen and separates the material into two streams: the under screen fraction - RBD (mainly containing organic material) and the over screen fraction - FSC (mainly containing dry material). The over screen fraction is sent to the subsequent metal separation and baling stages and then transferred to the RDF production plant. The under screen is destined for landfill or, in part, for the subsequent secondary maturation stage which is not mandatory to be realized.
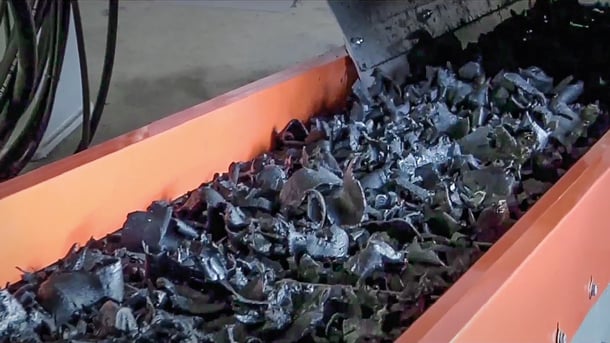
Baling
The oversize screenings (FSC), cleaned of metal fractions, normally sent in bulk to the RDF production plant, can alternatively be packed in bales through a baling and filming process. In the press, the material is conditioned in bales tied with wire and then a filming machine protects the bales with plastic film.
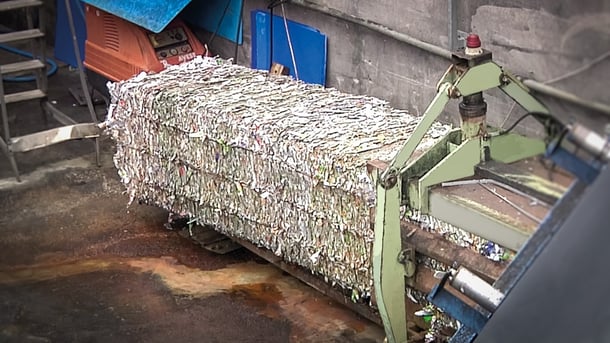
Metals separation
Separation of metal fractions on the over screen stream leaving the rotary screen. Ferrous metals, intercepted by a permanent magnet, and non-ferrous metals, collected with an eddy current separator (ECS), are subsequently sent for recovery.
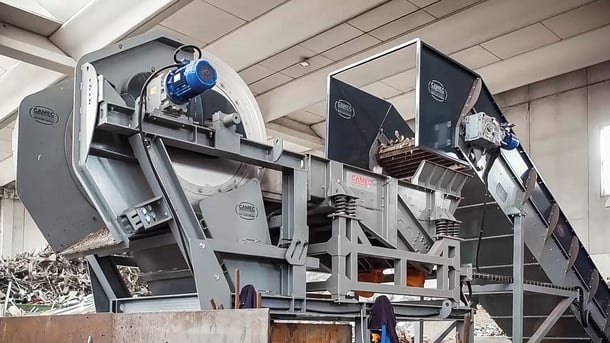
Final treatment
A further, non-compulsory, aerobic maturation and screening process, to which part of the under screen fraction can be submitted for the production of RBM for recovery.

Why you have to choose an industrial shredder?
The industrial shredding process is usually used for certain purposes, such as:
Space and volume savings before material is sent to landfill.
Material recovery through the recycling stages of metals and substances such as plastic and paper
Preparing the material for the combustion process
Sorting of waste in order to remove any component that may cause damage during a secondary process and separation of liquids from solids
The decision to use an industrial shredder can be guided by several factors, such as the need to dispose of bulky waste of various kinds. Shredders are also used for fragmenting common materials, such as plastics, and for preparing these materials for blowing and/or injection moulding processes. Industrial shredders also contribute to the preparation of plastics for extrusion processes.
All electrical and electronic equipment, which is classified as WEEE (computers, printers, photocopiers, cookers, dishwashers, mobile phones and other household electronic waste), as well as both domestic and industrial refrigerators and air conditioning equipment, can also undergo shredding processes. In general, the use of shredders contributes to the reduction of the size of the waste that will then have to be disposed of.
Of all the types of shredding, the most profitable in economic terms is the processing of plastics, the waste produced in the largest quantities on Earth.
Result
The result of the shredding process is usually a defibrated and irregular product in terms of size and quality. The product resulting from the shredding processes is usable for material recycling activities and not always for energy production.
Maintenance
Shredders’ maintenance mainly concerns the health of the blades that make up the different shafts that make up the structure. The more shafts are used to build the shredder structure, the greater is the number of blades that need to be polished and sharpened to keep the shredder running efficiently. Maintenance is usually one of the services provided directly by the shredder manufacturer.
In addition to maintenance, also services of customer care, after-sale and replacement of original parts can be provided.
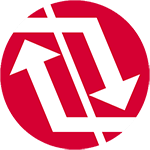
Discover the machines and turnkey plants for recycling different materials.
Tell us about your project
We supply the best technical solutions for your requirements